145 BMW Group Report 2024 To Our Stakeholders Combined Management Report Group Financial Statements Responsibility Statement and Auditor’s Report Remuneration Report Other Information Sustainability Statement the vehicle structure is pressed and shredded. This method guar- antees that today’s scrap becomes tomorrow’s raw materials. Insights gained at the Recycling and Dismantling Centre regard- ing the recyclability of components and materials are already be- ing integrated into the BMW Group’s product development pro- cesses. The BMW Group actively promotes recycling waste, including end-of-life vehicles, to keep materials in circulation for longer; this includes reusing them to produce new automobiles. In the reporting year, the materials from the vehicles (including motor- cycles) taken back by the Munich Recycling and Dismantling Center were 85% in material form1 and 95% including thermal processing1 recycled. This corresponds to a total scrapping weight for vehicles (including motorcycles) of 7,263 t1. In relation to sold automobiles and motorcycles, 85%2 of materials are re- cycled as stipulated by legal requirements (European End-of- Life Vehicles Directive ELV 2000 /53 /EC). At least 95%1, 2 of sold automobiles can be recycled (including thermal utilisation). Together with its national sales companies and importers, the BMW Group has already organised the return of end-of-life vehi- cles for recycling at more than 2,800 collection points in 32 countries. Research in this area is being stepped up in terms of the technology being used, processing efficiency, and costs in or- der to drive forward improvements in the recycling of end-of-life vehicles. The Car2Car project focuses on the recycling of alumin- ium, steel, glass, copper and plastic from end-of-life vehicles. This project began in January 2023 and is expected to run until December 2025. Together with representatives of the recycling industry, raw materials processors, and the scientific community, the BMW Group is leading a project to improve the quality of sec- ondary raw materials obtained from the recycling of end-of-life vehicles. Innovative dismantling and automated sorting pro- cesses will enable recyclable materials to be extracted to a far greater extent than previously. As part of the funding project, the BMW Group provided 433 end-of-life vehicles in 2023. In order to cover a representative range, various models out of the BMW Group’s own inventories are used from different BMW Group brands with combustion engines, plug-in hybrid systems, and all-electric drivetrains. In order to increase resource efficiency, avoid waste, and keep materials permanently and efficiently in the loop, the BMW Group is expanding its closed loops to include materials to which the Company has direct access. This includes recycled materials from production and the sales organisation. Selected materials from production and the sales organisation are returned to se- lected material suppliers on an ongoing basis. Production resi- dues generated during production can be on the one hand waste that can be processed and fed back into the production cycle as well as materials not considered as waste that can be reused di- rectly without the need for processing. This approach makes it possible to recover recyclable materials like steel or aluminium and make them available as raw materials for new production processes. The Chinese subsidiary BMW Brilliance Automotive Ltd. estab- lished a collection and recycling network for high-voltage storage (HVS) systems in 2022 to reduce the amount of primary materi- als used to produce new HVS systems. Work began on imple- menting a network of this kind in the European Union in the re- porting year. Similar networks will be gradually established over the next years in the USA and elsewhere. The BMW Group plans to use HVS materials as secondary material for the production of new HVS cells. In addition to actions in its own operations and in the value chain, the BMW Group supports innovation within the ecosystem by in- vesting in start-ups to test out new innovations with the aim of bringing them to the mass market. Through BMW i Ventures, the BMW Group has invested in a number of pioneering companies which focus on resource use and resource efficiency. Cyclic Ma- terials is developing a recycling process that reintegrates rare earth elements (REEs) into manufacturing. This innovation helps reduce the environmental impact of the global energy transition, as REEs play an essential role in the production of electrified ve- hicles. DeepDrive has created a cost-efficient, resource-efficient dual-rotor electric motor for vehicles. This motor increases the range of vehicles, delivers high torque density, and requires fewer natural resources. Lilac Solutions is developing an ion-ex- change lithium extraction technology with enhanced recovery rates, reduced impurities, and lower acid consumption. Man- grove Lithium is working on an electrochemical process for producing high-purity, battery-grade lithium hydroxide more cost-effectively. Our Next Energy is designing batteries with im- proved range and lower production costs. The BMW Group is also investing in research and innovation pro- jects to implement closed material cycles for certain product groups. The Circular Republic initiative, formed by the organisa- tion UnternehmerTUM and the BMW Group in 2023, focuses on the transfer of knowledge between the world of science and com- panies to promote the circular economy. During the reporting year, the BMW Group continued to promote various formats and joint projects. The BMW Group also focuses on the reparability of its manufac- tured products. During the product development phase, the BMW Group already places a strong emphasis on ensuring its products can be repaired and that the components in its vehicles can be disassembled in a non-destructive manner. 1 Additional disclosure, based on SASB ↗ SASB Index. 2 The percentages relate to the legal minimum requirements. In practice, higher recycling/recovery rates are also possible due to differences between vehicle versions and/or recycling/recovery pro- cesses.
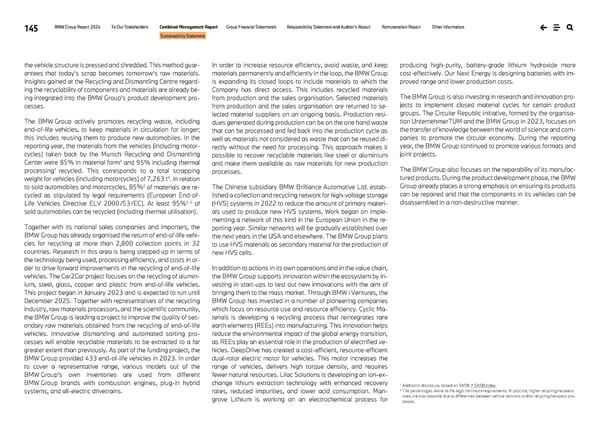