144 BMW Group Report 2024 To Our Stakeholders Combined Management Report Group Financial Statements Responsibility Statement and Auditor’s Report Remuneration Report Other Information Sustainability Statement The key actions driving the transition to a circular economy over the next years are outlined below. The BMW Group has launched some comprehensive prepara- tory initiatives in line with the "Ready for Circularity" principle. These will serve as a foundation for achieving closed material loops within the Company and across its value chain. These ini- tiatives span research and development, material procurement, supplier qualification, production, sales, the product use phase, and optimised use of materials and components at the end of a product’s life cycle. These initiatives focus on continuously en- hancing expertise and implementing measures related to vehicle development with the aim of increasing the use of secondary ma- terials and promoting circular economy-friendly product design. To advance a circular approach to product development, the BMW Group is committed to drawing up global strategies for ma- terials and components, with a particular focus on key materials such as steel, aluminium, battery materials, and thermoplastics. The BMW Group is building up its expertise and technical capa- bilities in the area of high-voltage storage (HVS) system recy- cling. This includes planning dismantling processes, testing re- cycling technologies, and integrating these insights into the bat- tery development process. To maximise resource conservation, the BMW Group is drawing up requirements for diagnosing and reusing used components, including high-voltage storage sys- tems. Another key initiative involves creating a data model based on digital twins, which is designed to facilitate material tracking from the end of a product’s life cycle and to ensure that the circular economy is transparent. This data model will also support the verification of secondary raw materials by suppliers and the ful- filment of disclosure requirements. We expect this data model to facilitate cross-Company data exchange in the medium term. Other examples of measures can be found at a vehicle project level. The ambitions of the BMW Group are further exemplified in the BMW i Vision Circular, which was unveiled at the IAA in 2021. This concept vehicle is mostly made from recycled or renewable raw materials. Some of the insights gained from this project are also being incorporated into the NEUE KLASSE. Beginning in 2025 for example, requirements for the proportionate use of secondary materials for battery cell materials such as cobalt, lith- ium and nickel will be imposed as soon as the contract is awarded. The NEUE KLASSE will also contain a higher propor- tion of secondary materials in other material groups such as steel and aluminium. Starting in 2023 with the BMW 5 Series, the BMW Group has disclosed the share of secondary materials in its new vehicles as part of life cycle assessments ↗ Vehicle footprint. Since 2024, the MINI Countryman has used cast wheels contain- ing 70% secondary aluminium, measured using the mass bal- ance method. For the BMW Group, circularity involves a comprehensive strate- gic approach. The circular economy is considered in the develop- ment of products, taking into account their recyclability at the end of their use phase (Design for Circularity). This approach follows key principles that promote the use of secondary materials and make vehicles easier to dismantle and recycle. With the “Design for Circularity” strategy, resource conservation is addressed during the vehicle development phase. This en- sures that circular economy principles are embedded in the prod- uct development process from the outset. Design for Circularity also lays the groundwork for recovering high-quality secondary materials at the end of a vehicle’s life. Components are designed and developed to include a defined proportion of secondary raw materials whenever possible. This approach also focuses on se- lecting recyclable plastic materials during the development pro- cess that facilitate a high-quality recycling process at the end of the vehicle's life. Improved dismantling concepts make it faster and more cost-effective to disassemble parts and reintegrate materials into the parts and materials cycle. Used components need to be refurbished and materials recycled to fully close the loop. A prime example of this holistic approach is the BMW Group’s remanufacturing process, where used parts are reconditioned and given a second life. The BMW Group has held a 50% stake in the joint venture En- cory GmbH since 2016. Encory provides comprehensive circular economy solutions, processes, and products in the aftersales sector. The company develops and implements logistics and consulting solutions, particularly for the collection, recycling, and refurbishment of spare parts. Whenever feasible and practical, defective parts are retrieved in select European markets (in ad- dition to some other markets, like China) in partnership with the joint venture. All suitable parts undergo a refurbishment process before being reintroduced into the spare parts cycle as remanu- factured components. Worn or damaged parts are disassembled by refurbishment partners instead of being completely replaced. Selected components are then cleaned, mechanically processed or replaced as needed, before being reassembled into a spare part. This process provides high-quality replacement parts that offer a number of advantages, such as reducing our use of valu- able raw materials, cutting emissions and saving energy. reduc- ing the environmental footprint of spare parts and helping the Group to manage resources responsibly. The BMW Group operates its own vehicle recycling facility at the Recycling and Dismantling Centre in Lohhof near Munich (Ger- many) to promote best practices in vehicle recycling while con- tinuously learning about and implementing the latest recycling technologies. Each year, thousands of vehicles are systemati- cally dismantled and efficiently processed at this site. Most of these vehicles are pre-production vehicle models that are no longer required for testing purposes. The focus of the entire pro- cess is on identifying reusable series components and disman- tling components that are suitable candidates for recycling. The disassembly process begins with deactivating restraint systems and draining fluids. Functional components used in mass-pro- duced models are then passed on to registered retail partners, eliminating the need for disposal. During the mechanical disman- tling of the remaining vehicle, materials like copper, which have a significant impact on recyclability, are separated out. Once the engine block and transmission have been removed, the rest of
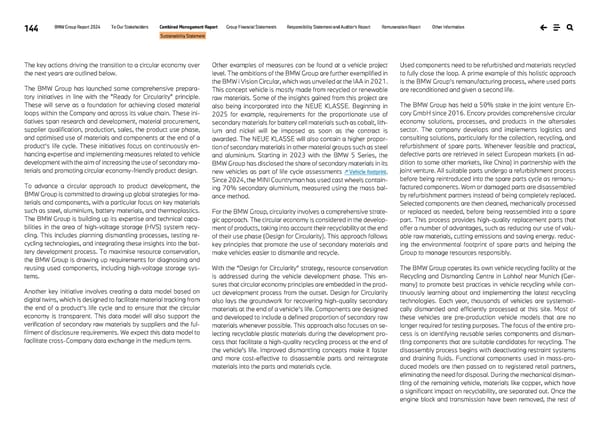